BOILER
GRAND PELLET
Essential information
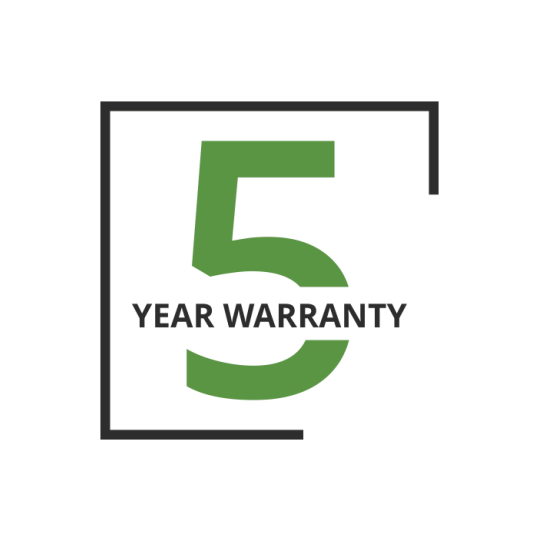
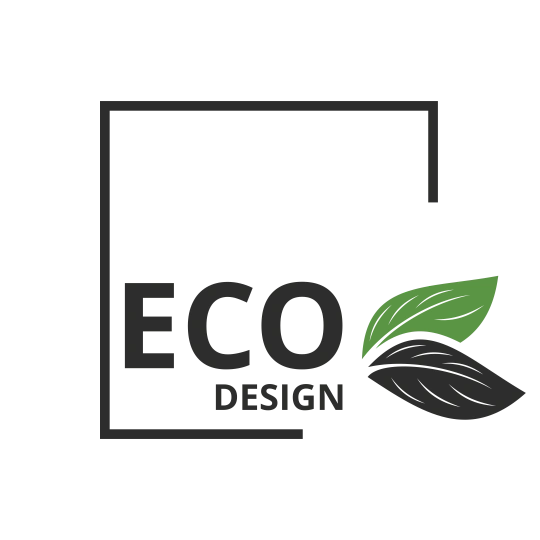
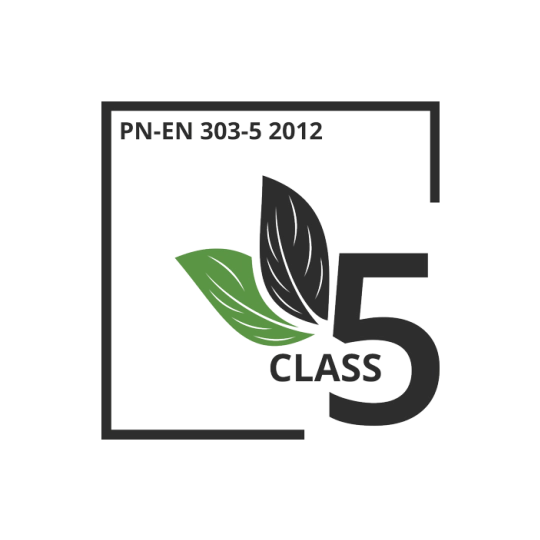
Available powers: 400kW I 500kW
Key benefits
Heat exchanger
Effective structure adapted to automatic cleaning of the exchanger. The design of the boiler exchanger ensures high heat removal from the furnace.
Flue outlet
The structure of the boiler has been designed in such a way that the flue outlet is at the rear. The use of such a solution in a central heating boiler allows the flue to be directly led out to the chimney.
Limit switch
Exhaust fan
The exhaust fan effectively supports the natural flue gas draft in the boiler.
Steel screens
Automatic feeder
Automatic ash removal system
The process of automatic ash removal consists in pushing the ash outside the boiler, into two specially designed containers. Both containers for collecting ash have wheels and a handle, thanks to which you can efficiently pull or lift them.
Swirlers
Swirlers installed in the convection channels, connected with the automatic cleaning system, effectively reduce the speed of the exhaust gas outlet. Thanks to systematic cleaning, the boiler maintains a constant high heat consumption through the water jacket. The use of automatic cleaning of convection channels contributes to the reduction of fuel consumption.
Boiler control
Key features:
Standard equipment:
Control the work, monitor, compare statistics thanks to the connection of the boiler controller with the internet module. Gain access to boiler control from a mobile phone, tablet or computer. The internet module is not only a remote control, it also records and registers the course of heating the house. Thanks to the ecoNET internet module (wired, wi-fi) you can gain control over your expenses and nothing will surprise you anymore!
Optional equipment:
Pellet burner
Self-cleaning PPW burner – for pellets
Quick firing up of the furnace and automatic cleaning of the furnace of ash. The burner is equipped with two automatic ceramic pellet igniters and has been designed for regular, automatic cleaning of ash. The design of the burner allows you to quickly reach a high temperature of the boiler. All functions of cleaning the furnace from ash and fuel dosage can be set in accordance with the current needs of the user.
Key features:
Ecological fuel such as pellets, also known as biomass, is produced by pressing wood waste such as sawdust or shavings. This completely natural fuel turns into biodegradable ash after burning.
Forget about manual boiler lighting. One click is enough and the automatic ceramic igniter ignites the fuel fed to the burner. Automatic igniter in conjunction with the RTC clock allows you to program the entire week of operation of the device. The device operation clock can be set separately for SUMMER and WINTER mode.
The burner is cleaned of ash on its own on a regular basis, which reduces the need for manual cleaning to a minimum. The use of this technology prevents clogging of the furnace chamber with ash, and also allows the burner to be kept in excellent efficiency.
Technical data of the boiler
PARAMETERS | UNIT S.I. | GRAND PELLET 400 |
Nominal thermal power | [kW] | 400 |
Boiler power range | [kW] | 120-400 |
Heatable surface* | [m2] | 1800-6000 |
Water capacity | [L] | 1750 |
Maximum working pressure | [bar] | 3 |
Maximum working temperature | [°C] | 80 |
Test pressure | [bar] | 4,5 |
Fuel tank capacity | [L] | 1000 |
Fuel tank capacity | [kg] | 600 |
Fuel | [-] | pellets Φ6-8mm |
Electrical connection | [-] | 5A; ~230V; 50Hz |
Electric power consumption | [W] | 685 |
Temperature controller setting range | [°C] | 60-80 (every1°C) |
Chimney draft required | [Pa] | 52 |
Boiler weight | [kg] | – |
* A new building with very good thermal insulation was adopted for the calculations.
PARAMETERS | UNIT S.I. | GRAND PELLET 500 |
Nominal thermal power | [kW] | 500 |
Boiler power range | [kW] | 150-500 |
Heatable surface* | [m2] | 2250-7500 |
Water capacity | [L] | 1950 |
Maximum working pressure | [bar] | 3 |
Maximum working temperature | [°C] | 80 |
Test pressure | [bar] | 4,5 |
Fuel tank capacity | [L] | 1000 |
Fuel tank capacity | [kg] | 600 |
Fuel | [-] | pellets Φ6-8mm |
Electrical connection | [-] | 5A; ~230V; 50Hz |
Electric power consumption | [W] | – |
Temperature controller setting range | [°C] | 60-80 (every 1°C) |
Chimney draft required | [Pa] | – |
Boiler weight | [kg] | – |
* A new building with very good thermal insulation was adopted for the calculations.
Certificates, class, boiler emission
PARAMETERS | UNIT S.I. | GRAND PELLET 400 |
Ecodesign | [-] | Yes |
Boiler class | [-] | 5 |
Energy class | [-] | A+ |
Seasonal particulate emissions | [mg/m3] | 19 |
Efficiency for nominal power | [%] | 90,7 |
Nominal emissivity of the particulate matter | [mg/m3] | 18 |
Efficiency at minimum power | [%] | 90,9 |
Minimum emissivity of particulate matter | [mg/m3] | 19 |
PARAMETERS | UNIT S.I. | GRAND PELLET 500 |
Ecodesign | [-] | Yes |
Boiler class | [-] | 5 |
Energy class | [-] | A+ |
Seasonal particulate emissions | [mg/m3] | 19 |
Efficiency for nominal power | [%] | 91 |
Nominal emissivity of the particulate matter | [mg/m3] | 18 |
Efficiency at minimum power | [%] | 90,5 |
Minimum emissivity of particulate matter | [mg/m3] | 19 |
Boiler dimensions
DIMENSION | UNIT S.I. | GRAND PELLET 400 |
A | [mm] | – |
B1 | [mm] | 1714 |
B2 | [mm] | – |
C1 | [mm] | 2310 |
C2 | [mm] | 2160 |
D1 | [mm] | 4721 |
D2 | [mm] | 4270 |
E | [mm] | 2284 |
F1 | [mm] | 1818 |
F2 | [mm] | 960 |
F3 | [mm] | 1686 |
F4 | [mm] | 165 |
G1 | [mm] | 340 |
G2 | [mm] | DN 100 |
G3 | [cal] | DN 100 |
G4 | [cal] | G 1 1/4 |
H | [mm] | – |
DIMENSION | UNIT S.I. | GRAND PELLET 500 |
A | [mm] | – |
B1 | [mm] | 1921 |
B2 | [mm] | – |
C1 | [mm] | 2310 |
C2 | [mm] | 2160 |
D1 | [mm] | 4721 |
D2 | [mm] | 4270 |
E | [mm] | 2284 |
F1 | [mm] | 1818 |
F2 | [mm] | 960 |
F3 | [mm] | 1686 |
F4 | [mm] | 165 |
G1 | [mm] | 340 |
G2 | [mm] | DN 100 |
G3 | [cal] | DN 100 |
G4 | [cal] | G 1 1/4 |
H | [mm] | – |
Boiler documentation
DTR instruction
Technical and operational documentation GRAND PELLET 400 | Download |
Technical and operational documentation GRAND PELLET 500 | Download |
Driver manual
PLATIUM PELLET controller manual | Download |
EcoDesign certificate
Etykieta energetyczna
A + energy class – 400 | Download |
A + energy class – 500 | Download |
Karta produktu zgodnie z rozporządzeniem UE 2015/1187
According to EU Regulation 2015/1187 supplementing Directive 2009/125 / EC of the European Parliament and of the Council – 400 | Download |
According to EU Regulation 2015/1187 supplementing Directive 2009/125 / EC of the European Parliament and of the Council – 500 | Download |
Karta produktu zgodnie z rozporządzeniem UE 2015/1189
Zgodna z Rozporządzeniem Komisji UE 2015/1189 z dnia 28 kwietnia 2015r. – 400 | Download |
Zgodna z Rozporządzeniem Komisji UE 2015/1189 z dnia 28 kwietnia 2015r. – 500 | Download |
Foreign sales
Paweł Czepiel
Export manager
Language: Russian, English
Monday-Friday (7:00 a.m. – 3:00 p.m.)
Phone:
+48 663 45 32 22
+48 85 711 94 54 ext. 17
E-mail:
p.czepiel@metalfach.com.pl
General contact:
Opening hours:
- Mon.-Fri. 7:00a.m.-3:00p.m.
- Phone: +48 85 711 94 54 int. 17
- E-mail: p.czepiel@metalfach.com.pl
General contact:
Service contact:
Opening hours:
- Mon.-Fri. 7:00a.m.–3:00 p.m.
- Phone: +48 85 711 94 54 int. 17
- E-mail: p.czepiel@metalfach.com.pl
Address data:
METAL-FACH Technika Grzewcza
Sp. z o.o.
- st. Sikorskiego 66, 16-100 Sokółka, Poland
- NIP: 545-182-60-12
- REGON: 523566030